ID : 4495
Control Log
A record of the robot's control, including movement of axes, current values, load ratios, etc.
This is useful in the following cases.
- Checking robot behavior within a specified range.
- Checking the age deterioration of the robot.
- Approximating the minimal load on the motor by predicting load ratios.
The control log recording time can be set by specifying the recording interval and number of records.
Recording can be made manually from the teach pendant or WINCAPSIII or through program operations.
The recording timing of the program is controlled using "SysLog.Ctrl.Start", "SysLog.Ctrl.Stop" and "SysLog.Ctrl.Clear" commands. For details, refer to "Logging" of FUNCTION GUIDE.
Grid Display
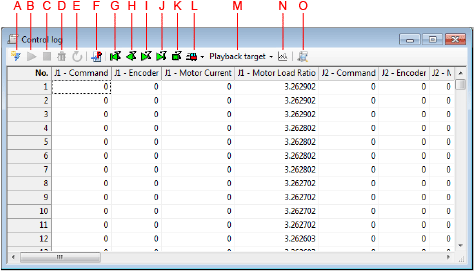
Graph Display
Description of the Drop-down Menu
A: Receive Button
This receives control log data from the robot controller and displays it.
B: Start Control Log Button
This starts or resumes the control log. SysLog.Ctrl.Start is executed.
C: Stop Control Log Button
This stops the control log. SysLog.Ctrl.Stop is executed.
D: Clear Control Log Button
This button clears the currently retained control log. SysLog.Ctrl.Clear is executed.
E: Update Control Log Button
This button updates the control log data simulating.
F: Jump to Source Code Button
This displays the source code for the selected log program.
G: Reverse Step in Button
This reproduction button plays back the control log, producing step-by-step robot motion in the reverse direction in the Arm 3D view.
H: Reverse Playback Button
This reproduction button plays back the control log, producing robot motion in the reverse direction in the Arm 3D view.
I: Playback Motion Button
This reproduction button plays back the control log, producing robot motion in the Arm 3D view.
J: Step in Button
This reproduction button plays back the control log, producing step-by-step robot motion in the Arm 3D view.
K: Stop Control Button
This button stops reproduction using the control log.
L: Speed Control
This controls the robot operating reproduction speed in the Arm 3D view subject to testing priority. There are two choices.
- Priority to collision detection
Robot movement is reproduced for each log data line. For collision detection you can prioritize collision determination with slowed down reproduction. - Priority to actual running times
Reproduction of operation matches the actual speed. (The collision may not be accurately determined.)
M: Playback target Button
Select the data for the playback of control log.
N: Graph Display / Grid Display Button
Switches the display style (graph/grid) for the control log data.
O: Control Log Analysis
The analysis results (predictive load ratio, maximum load ratio) are displayed in the output window.
- Predictive load ratio
Displays the predictive load ratio for a series of operations in the log range of processes. If the predictive load ratio exceeds 80%, an overload error is likely to occur. - Maximum load ratio
Displays the maximum load ratio in the log. At over 100% an overload error will occur.
P: Cursor Position
Moves the position of the cursor in the graph.
Q: Drawing Axis
Selects a data axis displayed in the graph.
R: Select Display Item
The checked items are displayed in the graph.
S: File / Line
Displays the File name and source code line at the cursor position.
T: Status
Displays the cursor position coordinates and the cursor position values of log data displayed in the graph.
The following items are recorded for the log data.
- Axis command values
Axis angles commanded by the controller in the specified recording interval - Axis encoder value
Current axis angle values (actual values) - Axis current values
Current values in the motors of the axes (compared with the rated value)In RC7M, the displayed value was a value compared with the overcurrent error detection level.
- Axis load ratios
Load ratios in the axes
ID : 4495