ID : 39
Robot Positioning Time
Refer to "Positioning Time of Each Axis" that includes positioning time data to be used in calculation of cycle times.
Positioning time refers to the time required from the start of robot operation to the arrival to the target point.
After the robot arm moves towards the target point and passes through it, vibration is dampened so that the robot arm is positioned at the target point as shown in the graph below. No vibration dampening time is considered in the graph.
The vibration dampening time is dependent on the weight of the end-effector and others. If the robot is to be used where overshooting or vibration dampening time particularly becomes a problem, carry out an adequate test for confirmation beforehand.
If acceleration begins before residual vibration of the robot arm stops, an overcurrent error (ERROR6120s, the first digit represents the axis number) may be displayed. In this case, take one of the following measures:
- Lower the deceleration of the preceding operation with a DECEL command to reduce residual vibration.
- Keep the robot waiting with a DELAY command until residual vibration stops.
- Lower acceleration with an ACCEL command.
Check the weights of the end-effector and workpiece sufficiently and run the robot with the optimum load settings. Improper settings may result in a robot failure.
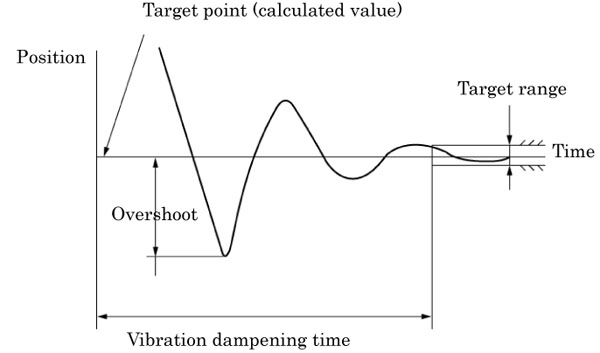
ID : 39