ID : 1576
Sample Program for Switching Defined Tool Coordinates
Execution of CHANGETOOL 0 will cancel the current tool coordinates definition and restore the default TOOL0 (mechanical interface coordinates).
TAKEARM statement automatically involves CHANGETOOL 0.
Sample Program
The example below shows a sample program that defines tool coordinates then releases them. End-effector 1 is placed at P1 and End-effector 2 is at P2.
![]()
|
End-effector 1
End-effector 2
Description of Program
(1) Defines,TakeArme
In the sample program, End-effector 1 and End-effector 2 are defined as TOOL1 and TOOL2, respectively.
Execution of TAKEARM automatically specifies TOOL0, so the robot will move to P1 (where End-effector 1 is placed) on the flange surface basis.
(2) Setting End-effector 1
As illustrated in the figure below, End-effector 1 will be mounted by "Set IO [104]." "Depart P,200" will make the robot apart from P1 and CHANGETOOL 1 switches the tool coordinates from TOOL0 to TOOL1.
(3) Releasing End-effector 1
To replace End-effector 1 with End-effector 2, first release End-effector 1 as follows.
"CHANGETOOL 0" will switch the current tool coordinates from TOOL1 to TOOL0. As shown in the figure below, the robot will move to P1 on the flange surface basis and release End-effector 1 at P1.
(4) Setting End-effector 2
As shown in the figure below, in mechanical interface coordinates, the robot will move to P2 where End-effector 2 will be mounted. "Depart P,200" will make the robot apart from P2. Then TOOL0 will be switched to TOOL2.
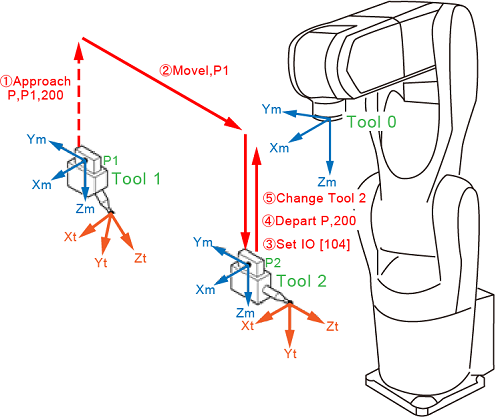
ID : 1576